Supply Chain Management
Principles and System of Supply Chain Management
To build a supply chain that is sound and sustainable, Tokyo Electron has formulated a procurement policy based on the laws, regulations and social norms of each country, as well as the RBA Code of Conduct, and together with its suppliers, is implementing activities based on this policy.
To identify issues in the supply chain from a variety of perspectives, we also value ongoing communication with diverse suppliers, including materials suppliers that handle parts and raw materials, staffing suppliers that provide services and logistics suppliers that handle physical distribution operations. Any issues which are identified are shared among the relevant departments which then work on improvement measures, under the supervision of the CEO. We will continue striving to create value across the supply chain by working to build relationships of trust with our suppliers, who support our business as partners, and by working together to deploy our operations in compliance with global standards.
The high-value manufacturing that the Tokyo Electron Group strives for is based on the functions of all materials and components that make up the products and the pursuit of high quality. We value communications with suppliers and seek to grow manufacturing on a global scale with our suppliers based on ongoing trusting relationships.
May 1, 2010 Established
- Compliance with Applicable Laws, Social Norms, and the RBA Code of Conduct
- We engage in procurement activities based on business ethics and with integrity, in compliance with the laws, regulations, and social norms of each country as well as the RBA Code of Conduct.*
The RBA Code of Conduct: Responsible Business Alliance Code of Conduct
https://www.responsiblebusiness.org/code-of-conduct/
A code of conduct drawn up by the RBA. The RBA Code of Conduct establishes standards to ensure that working conditions are safe, that workers are treated with respect and dignity, and that business operations are environmentally responsible and conducted ethically. - Priority on the Environment
- We conduct procurement with full consideration for reduction of environmental impact and protection of the global environment.
- Fair Business Practices
- We continuously seek high-value technologies and create broad opportunities for their business transactions based on the precondition of open competition.
- Partnership
- We prioritize relationships of trust based on mutual understanding with suppliers and conduct activities in the pursuit of mutual continuous growth.
- Information Management
- We properly manage the confidential information of suppliers that we obtain in the course of business
May 1, 2010 Established
September 1, 2024 Revised
The Tokyo Electron Group strives to comply with our Code of Ethics and the RBA Code of Conduct* to contribute to the development of society. We request that our suppliers understand the purpose of these policies and implement them and that their suppliers are also asked to understand and implement these policies.
We aim for sound and sustainable growth together with our suppliers.
- Compliance with Applicable Laws, Social Norms, and the RBA Code of Conduct
We request our suppliers to comply with the applicable laws and social norms in the countries and regions where they engage in business, as well as the RBA Code of Conduct. Please observe the following items in particular.- Prohibition of child labor, forced labor and labor involving debt bondage
- Management of appropriate working hours, breaks, holidays and leaves
- Appropriate payment of wages
- Respect for fundamental human rights, beginning with the prohibition of discrimination and inhumane treatment
- Thorough implementation of business ethics, beginning with the protection of intellectual property rights and the prohibition of false reports, falsification of records, bribery and conflicts of interest
- Compliance with export/import-related laws and regulations
- Prohibition of involvement with antisocial forces
The RBA Code of Conduct: Responsible Business Alliance Code of Conduct
https://www.responsiblebusiness.org/code-of-conduct/
- Considerations of Human Rights and Working Conditions
-
The Group promotes activities based on the Tokyo Electron Group Human Rights Policy. We request that our suppliers respect human rights and create a safe and healthy work environments in their business activities as well, based on their understanding of our Group’s Human Rights Policy.
Tokyo Electron Group Human Rights Policy - Response to the Responsible Procurement of Minerals
-
The Group sees our efforts with regard to the responsible procurement of minerals as part of our corporate social responsibility and promotes all efforts to eliminate any use of raw materials that utilize minerals which have been mined or extracted by illegal methods as well as components or parts that contain such minerals. To this end, we are implementing measures in accordance with the OECD Due Diligence Guidance for Responsible Supply Chains of Minerals from Conflict-Affected and High-Risk Areas. We request that our suppliers understand the situations pertaining to the procurement of minerals and cooperate in the survey for the responsible procurement of minerals.
- Environmentally Conscious Activities
-
In accordance with our Green Procurement Guidelines, we request that, together with the acquisition of ISO 14001 and the development of a structure for environmental conservation, suppliers also actively engage in the utilization and manufacturing of parts and materials that reduce environmental impact and that consider environmental conservation, the conservation of resources and the reduction of greenhouse gas emissions, and in addition, that they strive for biodiversity and forest conservation.
- Management System
-
We request that management systems are developed and continuously improved, including systems related to safety, health, the environment, product quality and labor, in accordance with the corporate procurement agreement or any specific agreements or arrangements with the Group.
- Technical Skills
-
We request that suppliers always strive for improved technical skills and technological innovations.
- Quality
-
We request that suppliers provide high-quality products and services which meet the specifications required by the Group by means of building quality during the design phase and strengthening change control.
- Supply, and Provide Systems
-
We request that suppliers provide a stable and flexible supply of products and services to deal with huge volatility in demand. Also, we request that suppliers prepare precautionary steps and continuity plans to reduce risks in the event of unforeseen situation such as disaster. In addition, we conduct BCP assessments on target suppliers and ask for their cooperation in these activities.
- Price
-
We request that products and services are offered at market-competitive and reasonable prices, and that continuous effort is made to reduce costs.
- Business Management
-
We request that sound and stable business management be implemented for the continuation of our business transactions. We also request that necessary financial and company information is disclosed.
- Information Security
-
In accordance with our Information Security Standards for Partners and Affiliates, we request that suppliers put a system in place that deals with the leaking of confidential information and cyberattacks, and construct an information security environment that appropriately manages and utilizes information. We also request for your cooperation in ensuring the security of our products.
To maintain a robust supply chain capable of supporting streamlined product manufacturing, TEL has instituted a procurement policy and established a system for administering fair procurement practices based on mutual trust with suppliers. Under the TEL Representative Director and President as the top of the procurement system, the manufacturing companies presidents’ council and the purchasing department manager council are convened to share information on various procurement issues. The council also serves as a venue to address current problems and discuss approaches to improve partnership with suppliers.
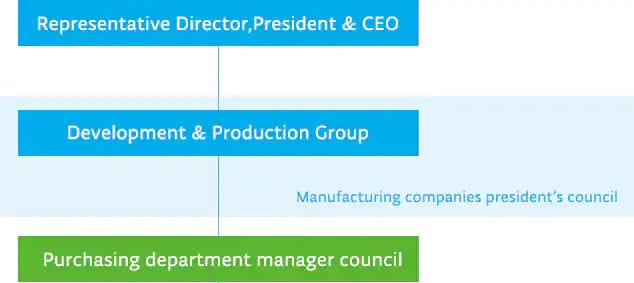
Sustainability Operations
Initiatives with Suppliers
To promote quality improvement of the Tokyo Electron Group and implement sustainability in our supply chain, it is essential to build strong partnerships with diverse suppliers, including materials suppliers that handle parts and raw materials, staffing suppliers that provide services, and logistics suppliers that handle physical distribution operations.
Before starting business with new suppliers, a Supplier Total Quality Assessment (STQA)-our Group’s in-house assessment system-is conducted via self-assessment to confirm the state of their product quality, costs, and information security. The assessment also includes CSR issues, including human rights, ethics, safety, and the environment. In addition, we conduct on-site audits to check quality, and if any risks are found, we explain to the supplier the problems and our expectations for the level of quality we require. After the supplier understands the issues, we ask that they plan and implement improvement measures. We also offer continual support to suppliers until all necessary improvements have been made. In fiscal year 2024, the percentage of new important suppliers screened using social criteria was 100%.
Furthermore, we conduct on-site audits once every three years at suppliers who manufacture important components and at suppliers where quality issues have been found.
Sustainability Assessment
We identify impacts to the business and various risks, and conduct screening of suppliers that require prioritized and continuous confirmation of their implementation states. In accordance with RBA auditing standards, we conduct the Tokyo Electron Group Supply Chain Sustainability Assessment each year in areas such as labor, health and safety, the environment and ethics since fiscal year 2014 for the materials*¹, staffing*², and logistics*³ suppliers selected through screening. We provide feedback on the assessment results to all suppliers who cooperated with the assessment and ask them to carry out any improvement activities required.
Materials suppliers: Suppliers accounting for more than 80% of our procurement spend (85% from fiscal year 2023)
Staffing suppliers: 100% of employment agencies and contracting companies (internal contractors)
Logistics suppliers: 100% of customs-related operators
Supply Chain Sustainability Process
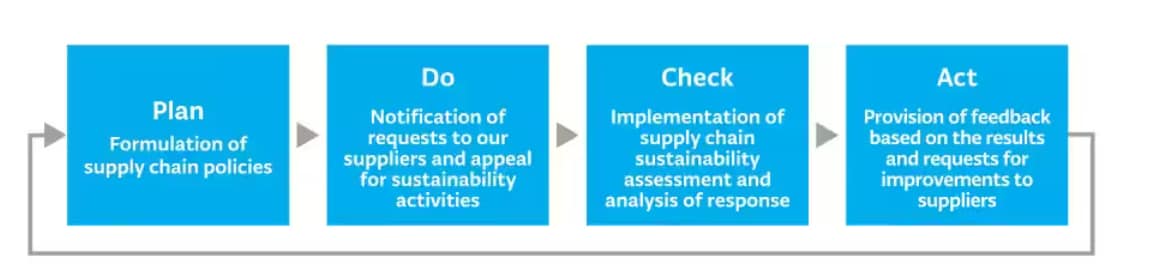
Annual Sustainability Goals and Results for Supply Chain Management
Percentage of suppliers for which supply chain sustainability assessments were implemented | Goal for FY 2024 | Results |
---|---|---|
Materials | At least 85% of procurement spend | Achieved at least 85% of procurement spend |
Logistics / 100% of customs-related operators | 100% | Achieved 100% |
Staffing / Employment agencies and contracting companies (internal contractors) | 100% | Achieved 100% |
In fiscal year 2024, we identified 704 suppliers that require prioritized and continuous confirmation of their implementation states. We conducted sustainability assessments for all these suppliers and received responses from all of them. The assessment results showed two suppliers with potential /actual risks that needed to be improved with priority, and we have requested to them to carry out corrective activities. In addition, we will confirm the implementation states and corrective action plans for each 56 suppliers in fiscal year 2025. We will provide support for corrective action as well as undertake monitoring.
Results of Supply Chain Sustainability Assessments Implemented in Fiscal Year 2024
Number of suppliers applicable for assessments | 704 |
---|---|
Assessment response rate | 100% |
Number of suppliers confirmed to have risks that needed to be improved with priority | 2 |
Number of suppliers requested to carry out non-conformance activities for risks | 2 |
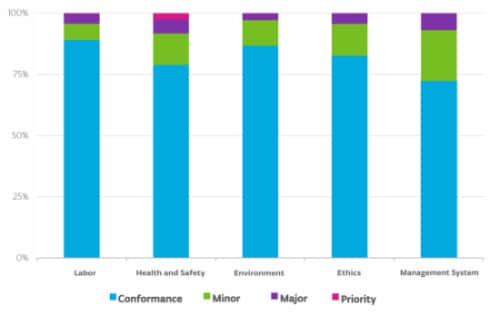
We also conduct briefings for suppliers regarding the results of each year's sustainability assessments. Together with explaining the latest assessment results and the points of corrective actions for each area, we also request suppliers to work on non-conformances. Furthermore, to ensure that all workers in our supply chain can work based on their own free will, we have explicitly stipulated our zero-tolerance policy for forced labor and bonded labor, and have communicated this to our suppliers.
In fiscal year 2024, we individually engaged suppliers that have been found to have non-conformances in employment-related expenses. We sought their understanding and remediation for the issues toward improvement.
Ongoing Efforts with Suppliers
Example initiative 1
Tokyo Electron Technology Solutions (Iwate) conducts activities to prevent quality issues jointly with suppliers. By implementing STQA for suppliers, we confirm their quality management systems and respond to. However, defects still occur in our manufacturing process, we launched a Supplier Quality Improvement Program (SQIP) to investigate and analyze the root cause of quality issues . In addition, under this program, for certain suppliers with high defect rates, we delve deep into defects that have already occurred to prevent reoccurrence and consider their repercussions, and focus on preventing other similar defects. The goal is to reduce the defect rate by 50% through ongoing efforts with suppliers and contribute to the further improvement of the relationships of trust with suppliers.
Example initiative 2
In fiscal year 2023, we underwent had RBA audit at Tokyo Electron Technology Solutions (Yamanashi), one of our main manufacturing sites in Japan, and have carried out the necessary corrective actions together with our suppliers. Going forward, we will further promote compliance with the RBA Code of Conduct through having our other major manufacturing sites undergo RBA audit, including those located overseas, and will expand sustainability initiatives throughout the supply chain. To promote such initiatives, we also conduct briefings on the RBA audit standards to our employees in charge of suppliers management to support the efforts of our suppliers.
Responsible Procurement of Minerals
We see taking action against conflict minerals obtained through illegal exploitation, which lead to human rights violations and poor working conditions, as our corporate social responsibility. Our resolute goal is to eliminate the use of raw materials made from these conflict minerals, as well as any parts or components containing them. In alignment with this way of thinking, we conduct surveys on the responsible procurement of minerals in accordance with the OECD*¹ Due Diligence Guidance for Responsible Supply Chains of Minerals from Conflict-Affected and High-Risk Areas. In fiscal year 2024, we set 3TG*² as the scope of minerals and conducted our 10th survey using CMRT*³, through which we were able to identify 238 smelters conformant with RMAP*⁴ (one of the standards used for determining whether minerals are connected with conflict). In addition, none of the materials we procured were found to contain 3TG involved in conflict. The survey results are shared with suppliers, and from fiscal year 2025, we will continue to conduct due diligence activities, including adding cobalt to the list of applicable minerals.
OECD: Organisation for Economic Co-operation and Development
3TG: Tantalum, tin, tungsten and gold
CMRT: Conflict Minerals Reporting Template. Survey format for reporting conflict materials, provided by the Responsible Minerals Initiative (RMI), which has established international guidelines on conflict minerals.
RMAP: Responsible Minerals Assurance Process. A program promoted and led by the RMI for auditing smelters/refiners to validate that they do not use conflict minerals.
FY2020 | FY2021 | FY2022 | FY2023 | FY2024 | |
---|---|---|---|---|---|
Number of identified RMAP conformant smelters
|
261 | 236 | 243 | 234 | 238 |
Rate of identification | 100% | 100% | 100% | 100% | 100% |
Procurement BCP
As part of our business continuity plans (BCPs), we collaborate with suppliers on ongoing disaster preparation. To properly grasp our supply chain, which is becoming more complex, we are using IT systems for the visualization of our supply chain. At the same time, we maintain a database of suppliers’ production sites so that if a crisis arises, we can promptly identify impacted suppliers and quickly collaborate in recovery efforts. There are now approximately 32,000 registered production sites as of fiscal year 2024, and post-disaster impact assessments (conducted when disasters occur) have been implemented three times. In addition, we conduct BCP assessments on our suppliers and analyze their responses to provide them with feedback so that they can promote improvements in areas of concern.
FY2020 | FY2021 | FY2022 | FY2023 | FY2024 | |
---|---|---|---|---|---|
Percentage of suppliers for which supply chain BCP assessments were implemented | At least 85% | At least 85% | At least 85% | At least 85% | At least 85% |
Rate of improvement after supply chain BCP assessment | 16.0 | 20.3 | 24.4 | 22.2 | 20.4 |
Environmental Initiatives
With the cooperation of our suppliers, we are promoting green procurement, prioritizing the purchase of environmentally friendly parts, products and materials. We also conduct surveys on product environmental laws and regulations for all parts and products purchased from our suppliers.
We also strive to establish and strengthen our environmental supply chain management through E-COMPASS initiatives. At the annual TEL E-COMPASS Day, we report on our E-COMPASS activities, provide the latest environmental information, and share information about activity policies. At the same time, we promote environmental initiatives across the entire supply chain together with our suppliers. We also grant the “Environmental Partners” to suppliers that especially cooperate in and contribute to our environmental efforts through E-COMPASS activities and certify them as "Green Partners."
On March 18, 2024, we held TEL E-COMPASS Day to provide a report on our environmental activities to suppliers.
This is the third iteration of this event. It was held in a hybrid format, with about 845 participants from our suppliers attending either in-person or online. The main theme of the event was TEL’s Net Zero 2040* target announced in December 2023. Featured presentations included a panel discussion, a report on the Group’s E-COMPASS activities, updates on the environment, and activity plans for the coming year.
TEL is targeting to reduce all its greenhouse gas emissions to net zero by fiscal year 2041, including Scope 1 and 2 emissions (i.e., emissions by TEL) and Scope 3 emissions (i.e., those by its supply chain).
Building of Partnerships
For daily communication and as opportunities for strengthening relationships with our suppliers, each of our manufacturing sites in Japan holds production update briefings twice each year. We also hold TEL Partners’ Day annually. Through these events, we communicate and share information about our management policy, market trends, business policies, and sustainability initiatives with our suppliers. We also present awards to recognize particularly excellent suppliers to express our appreciation for their daily cooperation, and at the same time, ask for our suppliers’ continued understanding of and cooperation in activities toward building a sound and sustainable supply chain. Overseas Group companies also create opportunities to share market trends, sustainability initiatives, and other such information with major suppliers to build strong partnerships and strengthen local supply chain management.
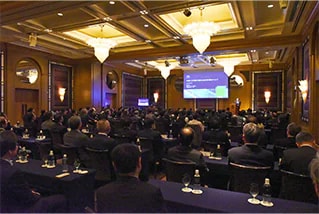
Source : Tokyo Electron
Example initiatives (Grobal)
Since fiscal year 2023, Tokyo Electron Taiwan has been organizing TEL Taiwan Partners’ Day to build partnerships and strengthen supply chain management in Taiwan. Besides sharing the Group’s management policies and trends in the semiconductor industry, this event expresses appreciation for daily business activities and asks for cooperation in various future initiatives in hope of developing the industry and contributing toward society and the environment.
In addition, Tokyo Electron Korea organized TEK Friends Day in fiscal year 2024 to share about the state of the Group’s business activities, initiatives for net zero and sustainability, and other such information to strengthen communication and collaboration with business partners.
Partnerships with Suppliers
In addition, Tokyo Electron announced the “Declaration of Partnership Building” in September 2022 to support the purpose of the Council on Promoting Partnership Building for Cultivating the Future, and in February 2023 Tokyo Electron Technology Solutions, Tokyo Electron Kyushu and Tokyo Electron Miyagi also announced, that is promoted by the Cabinet Office, the Ministry of Economy, Trade and Industry (METI), the Small and Medium Enterprise Agency (SMEA), and others.
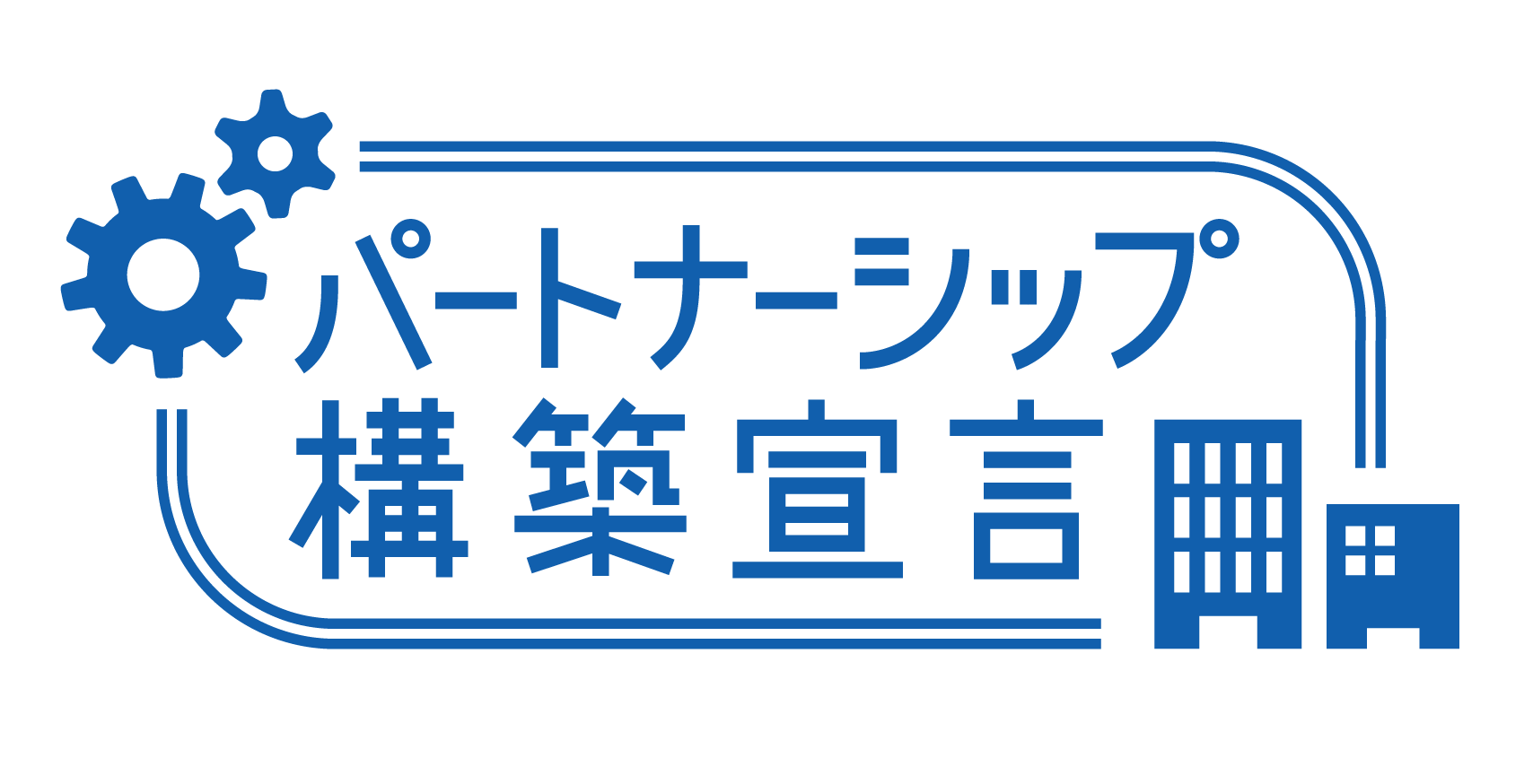
Implementing RBA Initiatives
In June 2015, Tokyo Electron Group joined the RBA*, a global initiative promoting supply chain sustainability focused on the electronics industry. RBA has stipulated the RBA Code of Conduct to promote improvements in labor, health and safety, the environment, and ethics through the supply chain. Based on the RBA Code of Conduct, we are working to build a sound supply chain while collaborating with other member companies.
In addition, to promote such initiatives, we also conduct briefings on the RBA audit standards to our employees in charge of suppliers to support the efforts of our suppliers.
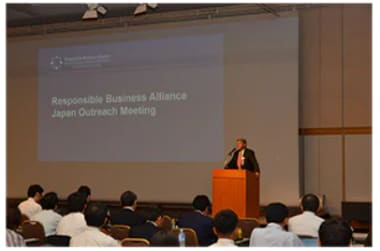
RBA: Responsible Business Alliance
Example initiative
In fiscal year 2023, we had Tokyo Electron Technology Solutions (Yamanashi), one of our main manufacturing sites in Japan, undergo audit based on the RBA Validated Assessment Program (VAP), and have carried out the necessary corrective activities together with our suppliers to achieve the highest recognition of platinum status.
The VAP audit evaluates if business activities are being properly conducted in accordance with the RBA Code of Conduct, confirming for proper management under the audit's sections of Labor, Health and Safety, Environment, Ethics, and Management Systems.
In preparation for the audit, corrective actions have been undertaken internally, such as developing evacuation routes and establishing lactation rooms and prayer rooms. At the same time, with the cooperation of suppliers, we promote various initiatives, such as the management of working hours and leave, bearing of employment fees, and multilingual support for pay slip.
Whistleblowing System for Suppliers
The Tokyo Electron Group has a supplier hotline for whistleblowing with the aim of early detection and the prevention of compliance issues.