Material issues
By realizing our vision and practicing our corporate philosophy, we aim to expand our profits over the medium to long term and enhance our corporate value continuously; to that end, we have positioned key items that should be given priority as our material issues, and these are reviewed each year. In the fiscal year 2024, we reviewed the content of our existing material issues to make them more detailed, and identified new material issues.
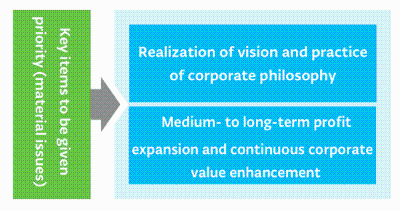
Material Issues Identification Process
We obtain the advice of a third party specialist regarding consideration of the process by which we identify material issues.
Prepare environment and determine issues | We analyze the status of social issues and the SDGs, business environments, the results of engagement with stakeholders*¹ and key risks in our business activities*² to determine issues that could become our material issues.
|
Prioritizing / Mapping | Determined issues are evaluated and mapped on two axes: “Importance to stakeholders,” which considers the impact on and interest of stakeholders, and “Impact on our performance and corporate value,” which aims to continuously enhance our corporate value.![]() |
Identifying Material Issues | We identified key items as material issues following discussions and decisions by the Corporate Officers Meeting, participated in by the CEO, and a report to and approval of the Board of Directors. In addition, we confirmed the material issues’ relation to key indicators for continuous corporate value enhancement*³ and the SDGs to be addressed. Furthermore, we clarified the main material issue initiatives in the value chain. |
Refer to Stakeholder Engagement
Refer to Risk Management
Refer to integrated report “Key Indicators for Continuous Corporate Value Enhancement”
Identified Material Issues
Material Issues | Significance as Material Issues | Main Initiatives | Relevant SDGs | ||
---|---|---|---|---|---|
Our Significance | Significance to Society | ||||
Climate Change and Net Zero | Reduce the environmental impact of businesses, products, and services to achieve net zero emissions | Reduce climate change risks and create new opportunities | ![]() ![]() |
||
Product Energy Efficiency | Achieve both the process performance and environmental performance of products | Preservation of the global environment by providing environmentally friendly products | ![]() ![]() |
||
Best Products with Innovative Technology | Establish superiority by creating high-value-added products with innovative technology | Promote innovation and development of society through the evolution of semiconductors | ![]() ![]() |
||
Best Technical Service with High-Value-Added | Expand business opportunities by providing advanced field solutions that solve customer issues | Improve semiconductor device yield and maximize equipment utilization rates | ![]() ![]() |
||
Customer Satisfaction and Trust | Pursue customer satisfaction and build relationships of absolute trust as a unique strategic partner | Maximize return on investment and expand mutual benefits through co-creation | ![]() ![]() |
||
Supplier Relationship | Carry out activities such as development, improvement, and quality improvement through collaboration | Maintain soundness and strengthen competitiveness throughout the supply chain | ![]() ![]() |
||
Respect for Human Rights | Reduce human rights risks and respect individual dignity in business activities | Solve issues such as discrimination, inequality, and those related to labor and safety | ![]() ![]() |
||
Employee Engagement | Create an environment where individuals can maximize their abilities and work actively | Provide various kinds of value that are beneficial to stakeholders | ![]() |
||
Safety First Operation | Achieve sustainable operations by putting safety first | Build a safe society | ![]() |
||
Quality Management | Pursue management efficiency through quality-focused operations | Create new value by strengthening competitiveness through quality improvement | ![]() |
||
Compliance | Comply with laws, regulations, industry codes of conduct, etc. as the basis for corporate reliability and sustainable growth | Improve compliance awareness and develop a compliance-oriented culture | ![]() |
||
Ethical Behavior | Strive to be a company with a strong sense of corporate social responsibility where our employees can take pride in their work and feel happy | Form a fair and orderly society | ![]() |
||
Information Security | Balance data utilization and information security by tackling cyberattacks, information leaks, etc. | Ensure information security without sacrificing convenience | ![]() |
||
Enterprise Risk Management | Aim for sustainable growth by appropriately responding to business risks and their impacts | Contribute to the medium- to long-term development of industry and society | ![]() ![]() |