Solutions that Create Value for Customers
Development of Global Operations
We established the Customer Collaboration Group and are working to further strengthen our customer support capabilities in order to be the sole strategic partner for our customers. The Customer Collaboration Group consists of the Account Sales Division, and the Global Sales Division. Major semiconductor manufacturers, who are our traditional customers, share the needs for next-generation leading-edge technologies in memory, logic devices, foundry and other fields, to the Account Sales Division, and this leads to R&D of new technologies, and the Global Sales Division responds to the needs of domestic and overseas customers that handle products for the rapidly growing Chinese market and the industrial IoT market.
These two divisions work closely with business units, development and manufacturing divisions, service divisions and overseas subsidiaries to develop global operations throughout our entire Group (=One-TEL), enabling us to quickly provide the technologies, services and solutions that our customers demand.
Proposing Customer Solutions Leveraging a Wide Range of Product Lineup
We are expanding the wide range of our product lineup, including equipment for the four sequential key processes of deposition, coater/developer, etch and cleaning in the front-end process, as well as equipment for testing and bonding/debonding processes in the back-end process. By leveraging this product lineup in our proposal activities, we will solve customers' issues and contribute to the manufacturing of highly competitive semiconductors.
In the front-end process, we are undertaking the development of equipment with innovative and extreme processing performance, centered on (1) deposition systems that can handle new materials and structure while utilizing batch, semi-batch and single-wafer characteristics and allow optimal film thickness and film quality control, (2) coater/developers for leading-edge EUV lithography, (3) etch systems that achieve precision processing of fine structure and processing of deep holes and trenches with high selectivity, and (4) cleaning systems that remove particles and residues—which are causes of lower yields—without causing the collapse of fine patterns. Possessing equipment with four sequential key processes allows us to propose solutions for issues faced by customers from a variety of approaches, including process integration based on an understanding of upstream and downstream processes. Specific proposals include processing methods in the deposition and etch of hard masks necessary for the processing of ultra-fine patterns as well as proposals for cleaning methods according to the residues generated after deep-hole etching and deposition methods—including preprocessing—according to the surface state after cleaning.
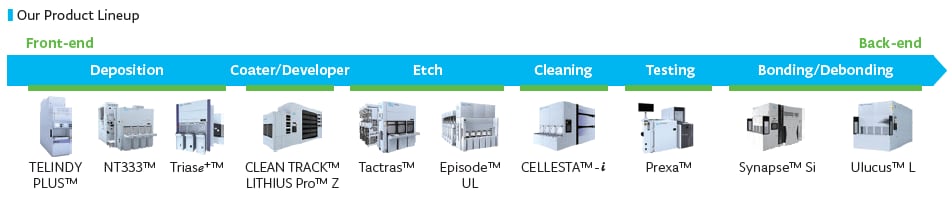
We also possess wafer probers used in wafer testing and bonder/debonder that realizes 3D packaging in the back-end process. In the future, there will be a demand for further improvements in the performance of semiconductors as well as scaling technology using cutting-edge nodes to improve the performance in generative AI services and expand the application range. To achieve this higher performance, the introduction of advanced packaging technology called Chiplet is accelerating, which combines individualized semiconductors. To meet these demands, we will proactively provide solutions for bonding processes necessary for both next-generation scaling technology and packaging technology, and introduce KGD* testing equipment, essential for Chiplet.
In addition to these measures, we strive to help customers improve productivity and quality in their development and manufacturing by providing optimal solutions that include remote support systems and software for maximizing equipment utilization rates. We are also continuously working to improve the performance of installed equipment to respond to customer requests for the manufacture of products that span multiple generations.
KGD: Known Good Die. Semiconductor chips with guaranteed quality, including reliability