Safety
Our Approach to Safety and Health
Tokyo Electron Group upholds the principle of "Safety First" as part of our Corporate Philosophy. In accordance with this principle, we give the highest priority to the occupational safety and health of all individuals, including management, employees, and the employees of business partners working within and outside the Group, as well as our suppliers and customers, in various business operations such as development, manufacturing, transportation, start up, and maintenance. We set goals to improve safety and good health and strive for ongoing, proactive improvements.
Our Safety Policy and healthy work environments are approved by the CEO and the corporate director in charge of safety and are applied to not only management and employees but everyone involved in our business.
November 27, 1998 Established
July 30, 2024 Revised
- Safety First
- Based on the principle of "Safety First," we strive to maintain and improve safety and provide healthy work environments for all employees, including the employees of partner companies working within and outside the Group, as well as suppliers, and customers.
- Legal Compliance
- We comply with laws and regulations, as well as international rules, guidelines and internal regulations pertaining to safety and health.
- Roles of Management, Supervisors, Employees, and Other Parties Engaged in Business Operation
- Management ensures operations are conducted with a "Safety-First" mindset, and the supervisors regularly audit safety and health management systems for continuous improvement opportunities. As a preventative measure to prevent work-related incidents, supervisors collect opinions from the site about safety in a timely and appropriate manner. Employees and other parties engaged in business operations are expected to always have safety at the forefront of their minds and are responsible for enhancing the work environment to ensure it is safe for all workers and visitors on site.
- Safety Activities
- We establish appropriate targets based on quantitative evaluation and analysis of safety activities and formulate implementation plans aligned with our priorities.
Employee representatives and relevant parties participate in Safety and Health Committee to discuss safety activities, share issues, and explore corrective and preventative measures. We work to deploy safety activities Group-wide and pursue ongoing improvements.
- We establish appropriate targets based on quantitative evaluation and analysis of safety activities and formulate implementation plans aligned with our priorities.
- Risk Assessments
- We identify risks involved in business activities, implement countermeasures, and evaluate their effectiveness.
We conduct quantitative analysis about hazard sources, scopes of impact, and frequency. We assess the probability and severity of incidents, including natural disasters and implement countermeasures based on priorities.
- We identify risks involved in business activities, implement countermeasures, and evaluate their effectiveness.
- Safety Training
- To raise employee awareness about safety and to build safer workplace environments, we develope training programs corresponding to the job responsibilities of employees and relevant personnel which are implemented Group-wide.
- Product Safety
- We adhere to international safety standards, country regulations and industry guidelines to provide customers with safe and reliable products.
- Equipment Safety Training
- We strive to prevent equipment-related incidents by providing appropriate equipment training for employees, other related parties, and customers to enable safe equipment operation. We actively disclose safety information and work to improve safety on a global basis.
- Communication
- We recognize that the basis of safety activities lies in fostering trust-based relationships. Management, employees, and related parties will strive for effective communication between all related people, including customers.
- Response to Disasters and Major Incidents
- In the event of extensive damage due to an earthquake, storm, other natural disaster, or an incidents, such as a fire, we will accurately ascertain the facts, prioritize protecting and rescuing human lives, and work together as one to quickly and calmly minimize losses, repair damage, and prevent recurrence. We have Business Continuity Plans in place in the event of a major incident and, will enact a Group-wide response under the direction of management, along with experts who will investigate the cause, and work to prevent recurrence.
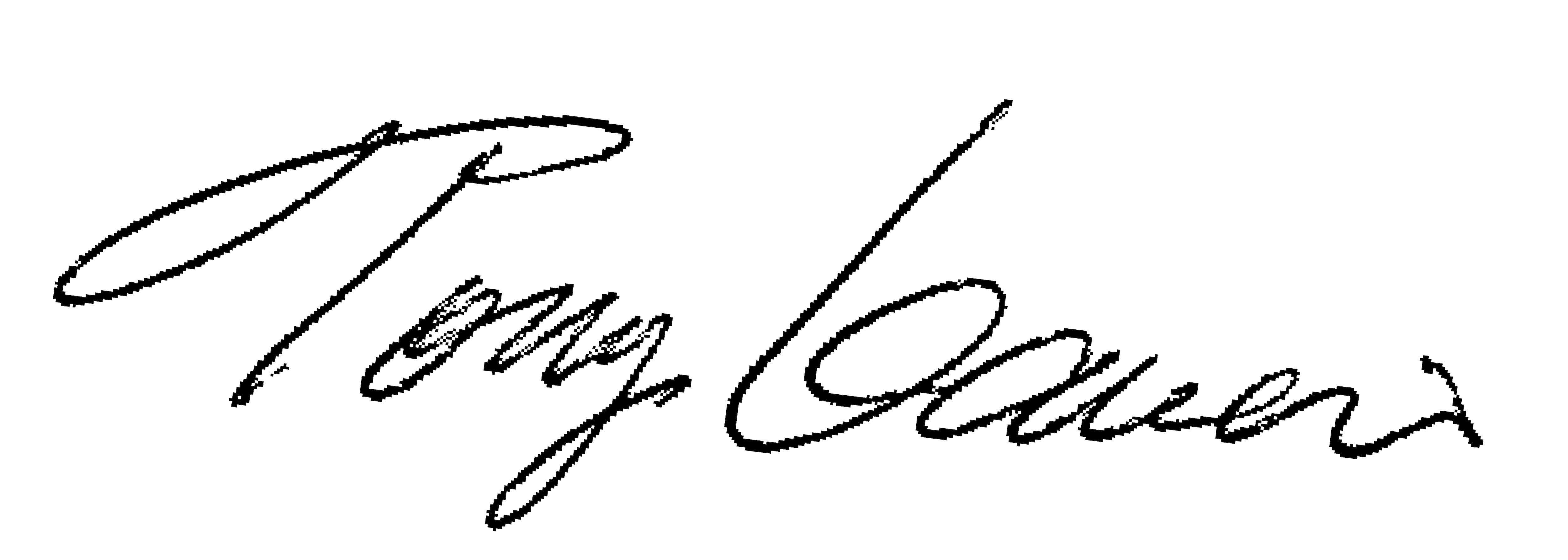
Representative Director, President & CEO
Tokyo Electron Limited
Based on a culture of "Safety First," we have established "Safety Policy" with approval of CEO, Corporate Officers Meeting and inform all employees of the policy.
We manage safety and health using an OHSMS*¹-based management system and progressively acquire ISO 45001*² and RBA*³ certification. We also implement the PDCA cycle to minimize the potential risk of work-related incidents and raise the standard of our safety and health management.
Example initiative
Tokyo Electron Taiwan has bolstered its occupational health and safety management system, making changes to risk assessments, revising in-house regulations, and strengthening sharing of incident case examples. The company acquired ISO 45001 certification in March 2024.
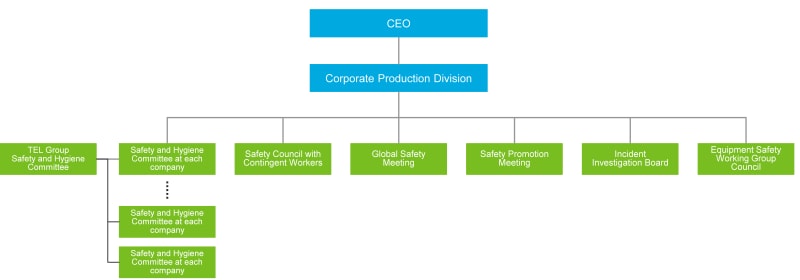
Occupational Health and Safety Management System. A management system to improve the overall level of safety and occupational health.
ISO 45001 is an international occupational health and safety standard. In the Tokyo Electron Group, Tokyo Electron Korea, and Tokyo Electron Taiwan have acquired ISO 45001 certification.*⁴
The Responsible Business Alliance (RBA) sets standards for ensuring that work environments are safe and that workers are treated with respect and dignity. In the Tokyo Electron Group, Tokyo Electron Technology Solutions Ltd. has acquired RBA certification.*⁴
As of April 1, 2024. Efforts to acquire certification continue.
Safety Activities
We establish appropriate targets* based on quantitative evaluation and analysis of safety activities and formulate implementation plans aligned with our priorities.
Employee representatives and relevant parties participate in Safety and Health Committee and other relevant meetings to discuss safety activities, share issues, and explore corrective and preventative measures. We work to deploy safety activities Group-wide and pursue ongoing improvements.
Achievement of the Medium-term Management Plan target—a total case incident rate (TCIR) of less than 0.10 workplace injuries per 200,000 work hours
Global Safety Council
Working together to reduce the number of incidents, safety representatives of every plant and every overseas affiliate gather once every six months to discuss matters such as the state and results of safety activities in each region, information on incidents, and recurrence prevention measures, and to share targets for the following term. This information is shared with contingent worker at meetings of the premises safety and health councils and Group-wide efforts are advanced.
Special Audits
To ascertain the realities of actual on sites, we visit Group-wide and customers to check on efforts relating to operating environments, equipment, and safety activities.
Incident Reporting System
Accessible to all employees, the TEL Incident Report System (TIRS)* is used to quickly share information with the relevant personnel, confirm the current situation, and deploy recurrence prevention measures. As a rule, incidents must be reported within 24 hours.
TIRS is Tokyo Electron Group’s TEL Incident Report System. The system is also used with all group company for report data aggregation, investigation of causes, analysis of trends and impacted personnel, and other activities as a recurrence prevention online system.
Near-Miss Incident and Hazard Reporting
TIRS is used not only for reporting incidents, but also to closely examine and specify near-miss incident and hazard reports in detail. A selection of reports are sent out to safety personnel worldwide in five languages once every two weeks to help prevent major incidents.
Risk Assessment and Stop Work Authority
Before we start to work, the work details and the risks are shared with all workers involved, and they each raise their safety awareness in an effort to prevent incidents. In addition to promoting guidance to safety management personnel, we are focusing on “stop work” to pause work and implement countermeasures when unexpected situations arise during works.
As a result of these ongoing initiatives in relation to reinforcing safety training and product safety design, our TCIR* reached 0.15 in fiscal year 2024, which is top class in the semiconductor production equipment industry. We will make further efforts toward achieving the target in our Medium-term Management Plan of 0.10 or less.
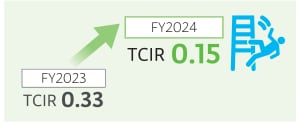
TCIR: Total Case Incident Rate. The number of workplace incidents per 200,000 work hours
Safety and Health Committee
Safety and Health Committee are convened monthly by employee representatives at each place of work. Participants discuss activities on workplace safety and employee health and safety and incorporate employees' opinion. Information from the Global Safety Meeting is also shared as a way of promoting Group-wide safety efforts. In addition, each place of work has in place systems enabling workplaces to resolve issues on their own, with representatives of each department regularly conducting safety patrol at least once a month.
Safety Patrols
Each place of work has safety activity systems enabling workplaces to resolve issues on their own, with representatives of each department conducting a safety patrol at least once a month.
Safety Training
To raise employee awareness about safety and to build safe workplace environments, we develop training programs corresponding to the job responsibilities of employees and relevant personnel which are implemented Group-wide.
Safety Foundation Training
"Safety Foundation Training" teaches the basics of safety to enable all employees to perform their operations safely in the workplace. Training programs are regularly reviewed to reflect analysis of the latest incident data. Employees undergo introductory training when they join the company and a refresher program every three years to maintain and enhance their safety awareness.
Example initiative
A "Safety training for second-year employees" program tailored to employees in their second year was introduced in fiscal year 2024 given the growing percentage in recent years of incidents involving employees with limited work experience, particularly those in their second year of service. The main purpose of this program is to remind employees of "Safety Foundation Training". It focuses on prevention of back pain, caused by lifting of heavy items, and accidental falls as these are the incidents most reported. Hazard prediction training is provided at the same time to enhance employees’ sensitivity toward safety matters.
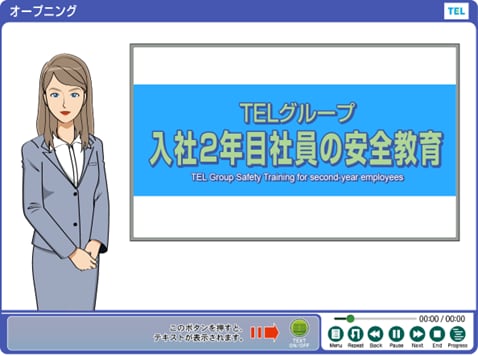
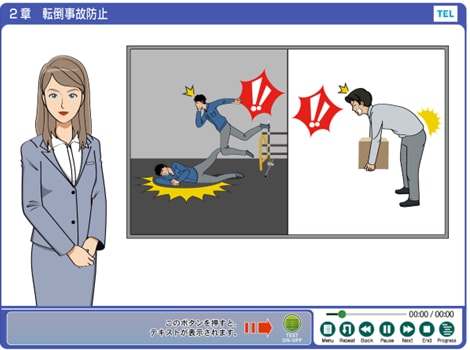
Safety Technical Training
"Safety Technical Training" is a more specialized program for engineers working on production lines or in cleanrooms. Refresher training is carried out each year. We also provide training about safety rules and legislation in each countries and regions for employees transferring overseas.
Country-Specific Statutory Training
For overseas transferees, the laws and regulations in their previous and future places of employment are compared, and additional safety education is added as necessary.
Enhancement of Training Facilities
Tokyo Electron Korea established the TEK Safety Academy in fiscal year 2024 to raise employee safety awareness and enhance their incident prevention skills through practical hazard experience. The slogan followed is “Watch, Try, Feel and Experience Safety First.”
Tokyo Electron Shanghai opened a new training center allowing practical training programs with a focus on experiential training (e.g. LOTO* simulation, heavy lifting).
LOTO: Lock Out Tag Out is a safety procedure used to prevent incidents and injuries that may be caused by the unexpected release of energy from facility or equipment.
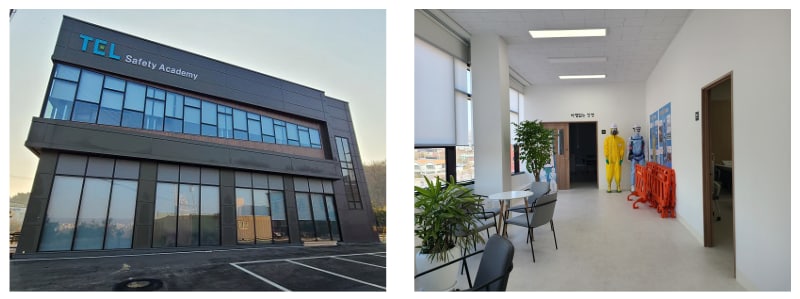
TEK Safety Academy
The facility houses a large conference room with a 60-person capacity
Product Safety
We adhere to international safety standards, country regulations and industry guidelines to provide customers with safe and reliable products.
Safe Design of Equipment
Taking the entire product life cycle into consideration, we carry out product risk assessments as early as possible in the development phase. We implement safe equipment design*¹ to reduce the risks posed to humans by incorporating the assessment results in the design. We conduct global surveys of increasingly strict laws and regulations and conduct compliance checks through third-party assessment bodies to ensure conformity with international safety standards and SEMI Standards*² on the equipment we ship. We have also established a system to comply with safety regulations of the regions where our equipment is delivered while working with overseas subsidiaries.
Intrinsically - safe design: A design concept that eliminates the cause of the machine’s harm to humans through the safety design of the machine
SEMI Standards: SEMI Standards are regulations formed by SEMI, an international industry body which serves manufacturers of semiconductor production equipment, display production equipment, PV power generation equipment, materials and the like, to unify all of these international industrial standards.
Equipment Safety Training
To entrench safe equipment design approaches in design through to manufacturing and servicing operations, we conduct safe equipment design training at manufacturing sites in Japan. We also promote our initiatives to prevent incidents, by providing our suppliers and customers with safety information as circumstances demand.
In recent years, it has become increasingly important for us to ensure compliance with international safety standards and guidelines early in the equipment design and development processes. Since fiscal year 2008, we have been offering its engineers web-based training on safe equipment design. Through risk assessment exercises and examples of actual incidents, the participants acquire basic safety knowledge for equipment design.
Feedback on Equipment Safety Specifications
If changes relating to safety specifications are requested by customers, or if an incident occurs as a result of equipment design, we provide the information to the Production Design Department as feedback and review to improve the organizational structures that will move forward with the necessary discussions as quickly as possible.
Customer Safety
We strive to prevent equipment-related incidents before they occur by providing equipment training to customers to ensure they use the equipment safely. We also proactively disclose safety information to customers and make company-wide efforts to improve safety.
Equipment Training for Customers
We establish training centers all over the world, mainly at our development and production sites, and provide customers with training on equipment operation and maintenance so that equipment can be used safely. To make training accessible even outside our training centers, we provide remote training* for most of our equipment. We try to enhance the training using video contents in some places, having prepared video captured from angles for easy viewing. In addition, we are working to improve the content and quality of not only remote training but also WBT by sharing the equipment and methods we introduced with each training center.
Remote training: A training course, although remote, where trainees interact with the instructor in real time while viewing actual equipment through their monitors
Provision of Safety-Related Information
We are committed to providing sufficient safety information on our products so that customers can safely use them. All our products come not only with a manual specific to the product specifications, but also a TEL Safety and Environmental Guidelines manual applicable to all our products. The TEL Safety and Environmental Guidelines manual is available in 12 languages* to ensure that customers around the world can understand the content accurately; it describes examples of potential risks associated with using our products together with the methods for averting those risks, as well as safety measures applied to products and recommended methods for product disposal, divided into such categories as chemical, electrical, mechanical and ergonomic.
If new safety warnings are identified after a product ships, we promptly report these to the affected customers.
We also make particular efforts to ensure that necessary information is communicated to customers to whom we deliver products that involve the use of hazardous chemicals or high-voltage electricity.
12 languages: Japanese, English, German, French, Italian, Dutch, Russian, Portuguese, Korean, Traditional Chinese, Simplified Chinese and Finnish
Communication
We recognize that the basis of safety activities lies in fostering trust-based relationships. Management, employees, and related parties will strive for effective communication between all people, including customers.
Incident Prevention Initiatives
Regular Safety Inspections
Regularly safety inspections are conducted throughout the Group using predetermined safety inspection items relating to work carried out at our own manufacturing locations and in-house management of our equipment. By revealing issues in work safety, training methods, safety management methods for equipment and the like, these regular inspections assist each Group-wide with their voluntary activities for maintaining and improving their safety environments.
Example initiative
In addition to inspection items for regular generators, other electrical equipment, rotating equipment, and motion transmission equipment, which require mandatory servicing and maintenance under law, Tokyo Electron’s safety inspections include infrared thermography to check for abnormal heat generation. These are carried out Group-wide.
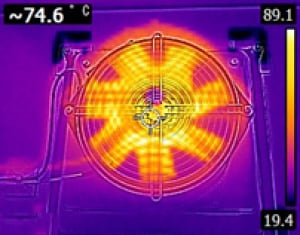
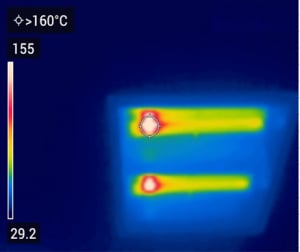
Response to Disasters and Major Incidents
In the event of extensive damage due to an earthquake, storm, other natural disaster, or an incident, such as a fire, we will accurately ascertain the facts, prioritize protecting and rescuing human lives,and work together as one to quickly and calmly minimize losses, repair damage, and prevent recurrence.
We have Business Continuity Plans in place in the event of a major incident and, will enact a Group-wide response under the direction of management, along with experts who will investigate the cause, and work to prevent recurrence.
For information on risk management and business continuity plans, see Risk Management in the About TEL section.