Customer responsiveness
Strong relationship based on trust / Sole strategic partner
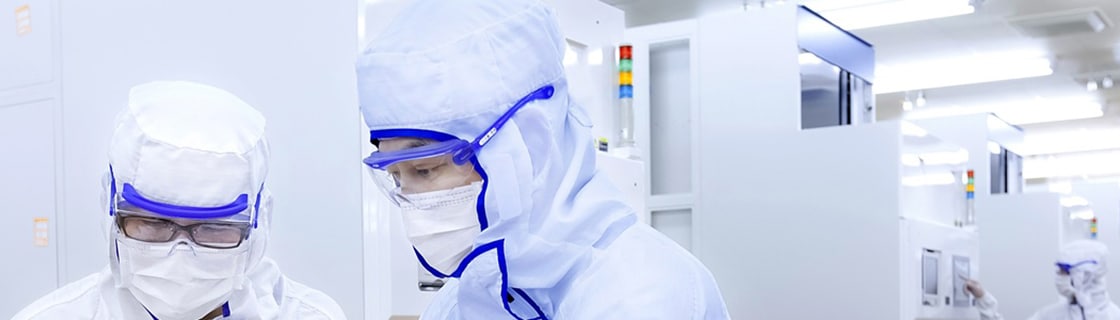
We will expand the following initiatives to build a "strong relationship based on trust" and be a "sole strategic partner."
- Contribute to customers that manufacture cutting-edge devices by maintaining an accurate and timely grasp on customer needs and providing innovative technologies for future generations
- Propose optimal solutions contributing to value creation for customers as a production equipment company with a diverse product range
- Make full use of state-of-the-art AI and digital technologies and provide high-value-added maintenance service that support the stable operation of equipment
- Continuously develop the PDCA cycle to further enhance customer satisfaction, a key management theme since our founding
SDGs initiatives
- Contribute to customers manufacture cutting-edge devices by maintaining an accurate and timely grasp on customer needs and providing innovative technologies for future generations
- Propose optimal solutions contributing to value creation for customers as a production equipment company with a diverse product range
- Make full use of state-of-the-art AI and digital technologies and provide high-value-added maintenance service that support the stable operation of equipment
- Continuously develop the PDCA cycle to further enhance customer satisfaction, a key management theme since founding