Field Solutions
Globalize Field Engineers and Strengthen Customer Responsiveness
Amid the expectation for rapid expansion of the scale of business, going forward, it is extremely important to increase field engineers, develop people that can promptly play an active role as well as effectively improve the skills of existing field engineers.
Our company establishes a Group-wide common skills management system that meets the standards of Semiconductor Equipment and Materials International (SEMI) and plans to upgrade skills according to the detailed goals established every year. The system helps us to improve the quality of the services we deliver to customers, by enabling the optimized deployment of human resources that utilize information about engineers' skills which have been managed in this manner.
Furthermore, we are expanding our program to reassign engineers who had undergone training at manufacturing sites in Japan for a fixed period to the field after their return to their companies, as part of our education for expert engineers for overseas subsidiaries. By participating in this program, engineers can not only deepen their understanding of equipment technology but can further improve their communication skills with engineers in the development and manufacturing divisions and business units. In addition, we offer high quality technical support that incorporates customer needs and implement programs to develop leaders in the field who can play an active role globally using high level skills.
In our equipment training geared toward our customers and our company engineers, we have established an environment where even more engineers can take courses by centrally managing information, such as training machines, instructor schedules and a record of training requests to courses taken, in a dedicated system.
We have also assigned engineers to our customers' onsite operations, and created a system where those engineers can be efficiently dispatched to where they are needed, regardless of country. We are proceeding with innovations to effectively implement education that is provided at the optimal time and short in duration, in which the whole structure is transparent, while promptly confirming the certifications and educational situations of our dispatched engineers to ensure high quality service.
In addition, we are undergoing renewals and expansion at each of our service sites and creating an environment where we can provide quick and efficient support to match the needs of our customers.

Support Services that Extend the Life Cycle of Equipment
As part of our efforts to have our customers use our equipment over a long period of time, we provide LEAP*, a support service that extends the life cycle of our equipment. Support for semiconductor production equipment typically ends seven to eight years after discontinuation of equipment due to the discontinuation of parts or the difficulty in maintaining safety and quality. For this reason, equipment for which support has ended is discarded and replaced with succeeding equipment. We now provide support service that makes the extension of the life cycle of equipment whose production was discontinued over 15 years ago possible by redesigning discontinued parts and restructuring and strengthening our support system including repairs.
We support customers who have difficulty with replacement with newer equipment due to restrictions on change management of equipment specifications or operations, or who hope to continue using their equipment. Through this support, while implementing initiatives that reduce equipment disposal and environmental impact, we contribute to the continuous operation of customers' equipment over a long period of time.
LEAP: Lifecycle Extension and Availability Program
Promotion of High-value-added Services
We have built a global support system by highly specialized engineers, establishing Total Support Centers (TSCs) in Japan, the United States, China and Europe.
By accumulating large amounts of operation history, such as equipment support in everyday activities in Service CRM, which is centrally managed globally, as well as creating equipment records and building troubleshooting search tools as knowledge management activities, TSC and onsite field engineers use these tools to provide prompt and high-quality services to our customers. We are also developing a system that centrally manages internal operation procedures created by field engineers onsite to improve the efficiency of procedure creation, quality, and searchability of operation procedures, and are preparing to roll them out globally. In addition, we strive to resolve our customers' various issues through the use of TELeMetrics™, a remote maintenance service, and remote support tools.
Our company provides several contractual services for the stable operation of equipment, such as services in which our field engineers are stationed at customers' manufacturing sites to maintain their equipment, as well as a comprehensive contractual service (TEL Service Advantage Premium) in which we offer pay-as-you-go or flat-rate maintenance services, supply maintenance/consumable parts and repairs in an integrated manner.
Furthermore, to shorten trouble resolution time and stabilize process performance, we aggregate and analyze data output from equipment, predict the timing of failure of major parts and suggest replacements in advance so that we can continually implement activities that lead to improved equipment utilization rates.
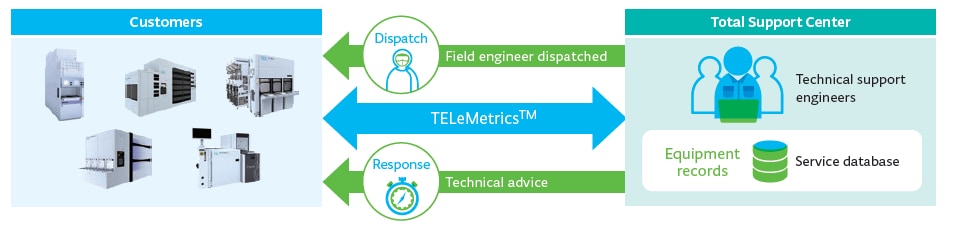
Engineer’s Skill Up
In fiscal year 2019, we established our training operations center to enhance the training structure and promote globalization of field engineers. The center establishes a company-wide common skills management system that meets the standards of SEMATECH (a U.S. consortium for the joint development of semiconductors). The system helps us to deploy the most suitable human resources to provide customers with service based on an objective measurement of the skills of our engineers.
In fiscal year 2021, we began providing education for expert engineers to improve the skills of engineers at our overseas subsidiaries. The education includes training programs that enable technical support engineers from overseas to learn not only technical support but also acquire advanced skills related to development in a practical manner at our manufacturing sites in Japan. Furthermore, we also conduct training for field engineers of our Global Data Engineering Team, established in fiscal year 2021, to develop data analysts specializing in digital transformation (DX)*.
In fiscal year 2022, field engineers who have acquired DX skills developed a program for the continuous improvement of business operations and are rolling it out globally. By linking this program to the field information database, it became possible to automatically update, analyze and visualize field information.
Digital transformation: Refer to Strengthening of Product Competitiveness through Digital Transformation (DX) and refer to Higher Productivity through Digital Transformation (DX)