Productivity Improvement in the Value Chain
TEL Quality Global No.1
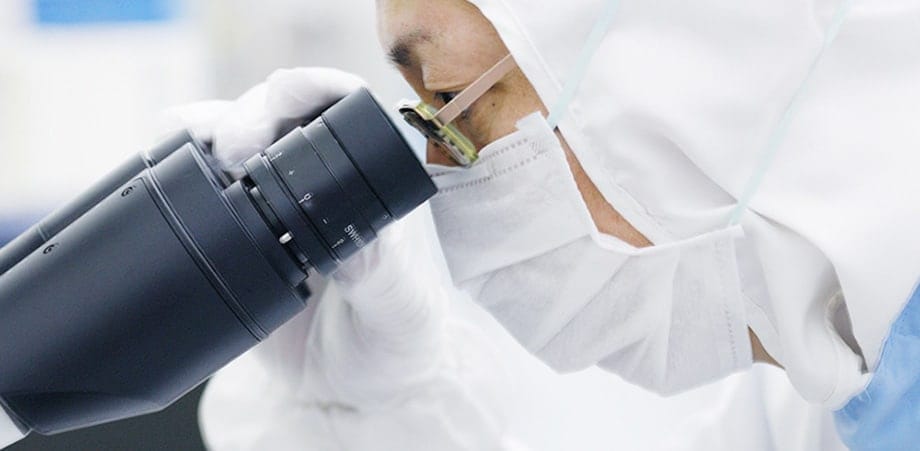
Knowing our customers' real needs enables us to attain world-leading product quality.
Approach to Quality
Tokyo Electron defines it's approach to quality in the following way: “The Tokyo Electron Group seeks to provide the highest-quality products and services. This pursuit of quality begins at development and continues through all manufacturing, installation, maintenance, sales and support processes. Our employees must work to deliver quality products, quality services and innovative solutions that enable customer success.” We strive to implement this policy.
We strive to implement self-process assurance systems*1 by carrying out strict quality-related risk management and development/design inspections beginning at the development stage, and also by ensuring thorough verification of customers’ operations using simulations. We have also built an important component traceability system to strengthen our information environment.
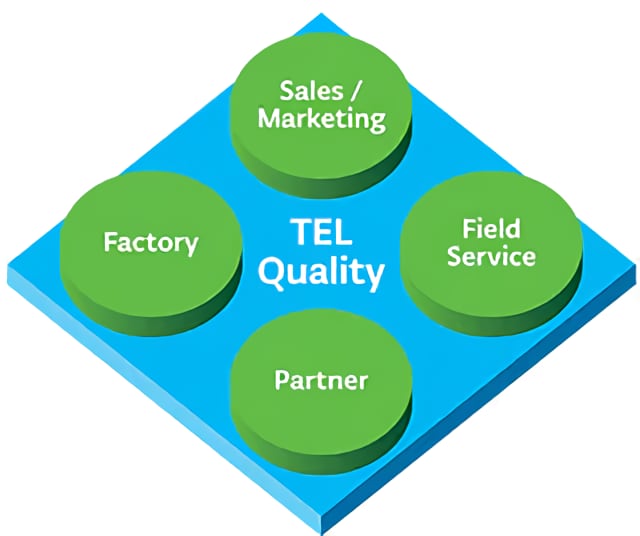
Specifically, to prevent various types of non-conformances, we built a system that allows One Platform*2 to view information such as past problems, adjustment values used during manufacturing and assembly and important component inspection information from suppliers, and have successfully strengthened our risk management (FMEA*3).
By thoroughly implementing these self-process assurance system and prevention measures, it creates time for employees to focus on high-value-added business operations and promotes initiatives for Shift Left*4 (front-loading).
Self-process assurance systems: Refer to Ensuring Self-process Assurance Systems and Promoting Shift Left
One Platform: A platform that makes it possible to easily view multiple different systems as seamless information sources, in order to effectively and efficiently achieve traceability. Refer to Initiatives for Higher Productivity
FMEA: Failure mode and effects analysis. A method to identify, prevent and mitigate risks in advance.
Shift Left: Refer to Shift Left and refer to Ensuring Self-process Assurance Systems and Promoting Shift Left
- Quality Focus
- Focusing on quality to satisfy customers, meet production schedules, and reduce required maintenance even with temporary cost increases.
- Quality Design and Assurance
- Building quality into products and assure in-process quality control, from the design and development phase throughout every process.
- Quality and Trust
- When a quality-related problem occurs, working as a team to perform thorough root cause analysis and resolve problems as quickly as possible.
- Continual Improvement
- Ensuring customer satisfaction and trust by establishing quality goals and performance indicators and by implementing continual improvement using the PDCA cycle.
- Stakeholder Communication
- Listening to stakeholder expectations, providing timely product quality information, and making adjustments as needed.
The quality policy listed here is shared by all TEL Group companies. The policy is linked to the three focus areas (i.e., enhancing product competitiveness, reinforcing responsiveness to customers, and strengthening earnings power) for attaining the medium term management plan’s GT2025 goals, and it has direct bearings on each employee’s action. That is why the policy governs not only our manufacturing plants but also our head office and group companies’ sites in Japan and abroad. A TEL Quality Policy poster has been produced in Japanese, English, Chinese (simplified characters), and Korean and distributed to be posted at TEL Group sites throughout the world.
To provide consistent, high-quality products, we have built and are implementing quality assurance systems under the leadership of the CEO. All manufacturing companies in the entire Group have attained certification in the latest quality management system, ISO 9001. In addition, we conduct regular internal audits as well as neutral and fair audits by third parties for each manufacturing company of the Group to contribute toward maintaining and improving our quality management systems.
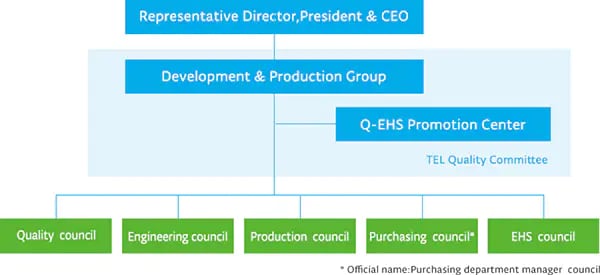
ISO 9001 Certified Plants and Offices
Company Name | Plant/Office Name | Certification Number | Certification Date |
---|---|---|---|
Tokyo Electron Technology Solutions | Fujii Office/Hosaka Office | 00225-1994-AQ-KOB-RvA | Sep.1994 |
Tohoku Office | Dec. 1994 | ||
Tokyo Electron Kyushu | Koshi Office | 5569-1997-AQ-KOB-RvA | Mar.1997 |
TEL Magnetic Solutions | - | IE09/66498 | Nov.2009 |
Tokyo Electron Miyagi | Taiwa Office | 02609-2012-AQ-KOB-RvA | Sep.2012 |
Tokyo Electron Korea | Balan Plant | QSC1680 | Sep.2011 |
TEL Manufacturing and Engineering of America | Chaska Office | FM586277 | Mar.2013 |
Tokyo Electron (Kunshan) | - | 260147-2018-AQ-RGC-RvA | May 2018 |
Process Improvement Activities
The production sites of our customers require limited variations in quality between equipment, accurate process repeatability and high productivity. To provide products that match such customer needs, we focus on process improvement activities (PCS*1) using a statistical method.
We create control diagrams for the information of various types of critical components (components directly in contact with wafers and components that directly affect the process of systems, such as components that transfer mechanical, thermal, electrical or electromagnetic energy to wafers) and analyze variations to quickly detect and respond to changes in manufacturing processes. By undertaking such PCS activities together with suppliers handling specific critical components, we work on the suppression of component quality variability and maintenance/improvement of manufacturing processes that produce quality products to help provide products surpassing customer expectations.
In addition, manufacturing processes handling new critical components need constant review and improvement. Our products comprise several tens of thousands of components, and the task to select specific components from these and carry out regular aggregation and analysis require many man-hours.
To optimize and streamline this task, we reexamine our operational flow, including the adoption of automation, and improve our systems by collecting information from customers, holding discussions among our manufacturing sites in Japan and interviewing our suppliers. By continuously carrying out these activities that are based on the concept of Shift Left, we are striving to improve our productivity further.
Example Initiatives
At Tokyo Electron Technology Solutions (Tohoku), design of experiments*2 based on statistics is used to establish quality metrics for critical components and the level of quality activities is being improved together with suppliers.
The best quality metrics established using the designs of experiments are set as the targets. Conditions that give rise to variations in inspection, adjustment and other values in the manufacturing processes of critical components are strictly managed using PCS activities to seek accuracy and stability in the manufacturing processes.
In the future, we will promote the automation of processing—from collection to assessment—of suppliers’ data regarding quality and detect the state of quality in real time to further improve the manufacturing processes of critical components.
PCS: Process Control System
Design of experiments: A branch of applied statistics that aims to design efficient experimental methods and properly analyze the results
Ensuring Self-process Assurance Systems and Promoting Shift Left
In order to improve the quality of products, it is important to prevent non-conformance from occurring in upstream processes and to ensure thorough quality control in each process so that nonconforming products— if they occur—are not allowed to flow into later processes. From this perspective, we promote activities focused on self-process assurance systems. In particular, we aim to further improve quality by implementing thorough risk detection and mitigation measures (FMEA*1) from the initial stages of product design, as well as carrying out thorough inspections in each process and conducting verification using simulation.
These activities for in-process quality control make it possible to create high-value-added technologies and products in the upstream processes by improving the precision of each process and reducing reworking costs*2, and at the same time, lead to the promotion of the Shift Left*3 concept.
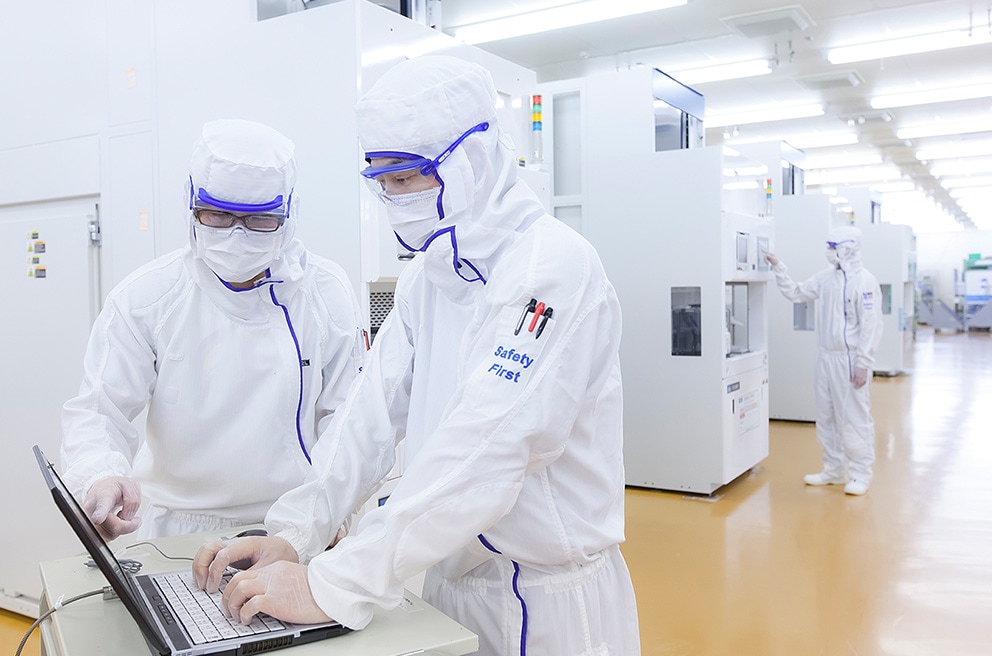
We are also promoting Product Lifecycle Management (PLM) by using in-process quality control to comprehensively manage and analyze all processes from product planning, development, design and production through to service in an effort to facilitate the earlier release of products, enhance operational efficiency, improve quality and reduce costs.
FMEA: Refer to Approach to Quality
Reworking costs: Costs incurred by going up the chain of processes and reworking when there is non-conformance
Shift Left: Refer

Measures to Prevent Quality Problems from Occurring and Recurring
To comply with ISO and EN*1 safety standards and achieve higher safety levels, we have established its own design rules for each product. At the same time, we have developed systems for manufacturing products, which include safety considerations. We also have other systems in place for responding to issues such as equipment design and production non-conformance and any occupational incidents.
In the event of an incident, we use our TIRS*2 incident reporting system to distribute information to safety and quality personnel in each division and officers and management, including senior management. An incident investigation is also conducted immediately to identify the cause and plan preventive measures.
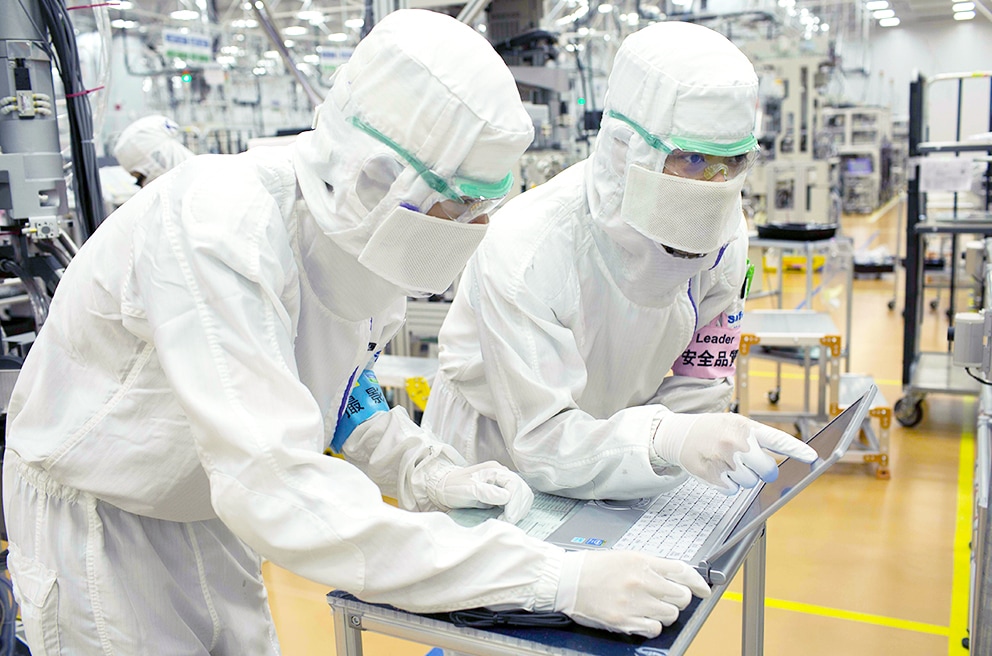
We use a proprietary system called QA-BOX*3 to share information on equipment quality and any major non-conformance across all quality departments in accordance with our operating rules. Measures obtained from the results of an incident investigation are promptly applied, not only to the problem equipment but also to relevant equipment operated by other customers. At the same time, after finding the root cause, revisions are also made to the current design standards and processes to perpetually prevent the occurrence of major non-conformances.
For departments that become subjects of incident investigations, we validate repercussions to other equipment and commonalities and share the issues and countermeasures at regularly scheduled QA-BOX meetings together with the heads of quality assurance divisions. This allows us to examine various approaches to prevent similar non-conformances. The common policies determined at the regular meetings are quickly deployed across the entire Group and reflected in the respective equipment. This helps to reduce nonconformances caused by equipment.
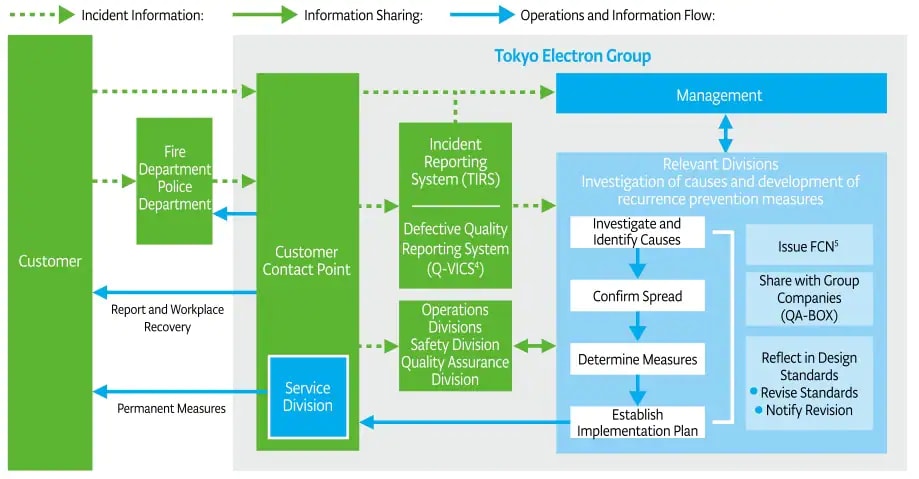
EN: European Norm. Uniform standard for the European Union complimenting parts of technical standards not stated in European Commission directives (“New Approach” directives)
TIRS: TEL Incident Report System
QA-BOX: Tool for the sharing and horizontal deployment of important quality-related information within our Group companies
Q-VICS: Quality Valuable Information Chain System
FCN: Field change notice. Refers to the general recall notice
Initiatives with Suppliers
Continuously improving quality based on strong partnerships with suppliers is essential for providing high-quality products quickly to the market. Since fiscal year 2001, we have conducted our unique Supplier Total Quality Assessments (STQA) in an effort to ensure our suppliers properly understand the level of quality expected from them.
Before starting a new business with suppliers, we conduct an STQA via self-assessment to evaluate their product quality, costs and information security. The assessment also includes their corporate social responsibility initiatives, including human rights, ethics, safety, and the environment. If a risk is identified in this assessment, we visit the supplier and confirm the area of non-conformance on-site.
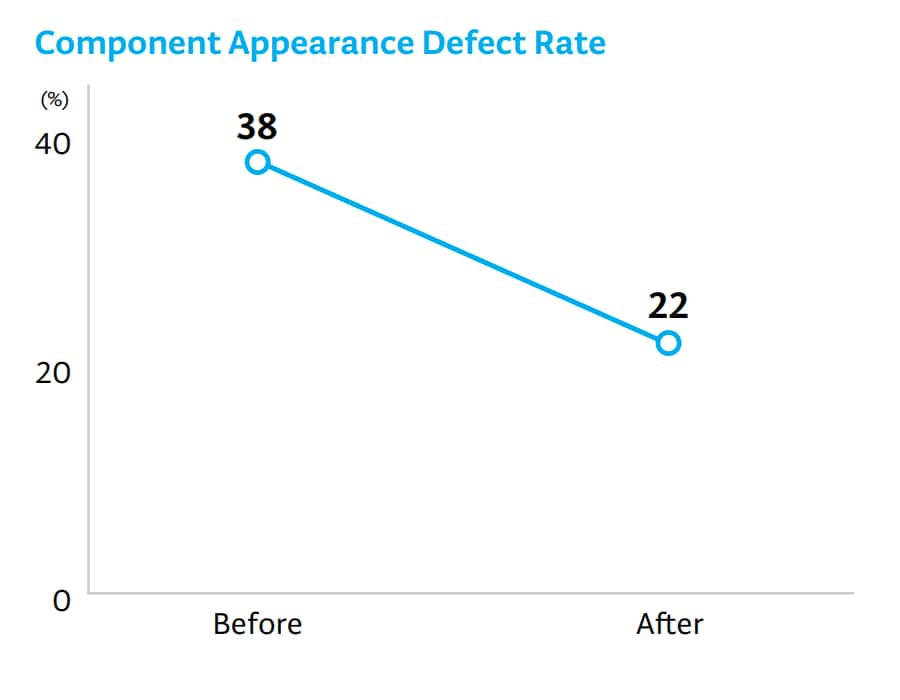
Once our approaches to quality and other important related issues have been shared with the supplier, we request that they plan and implement improvement measures and provide continuous
support until all of them have been completed. In addition, we also conduct audits once every three years for suppliers who handle important components and for suppliers where quality issues have been found.
We also hold regular meetings with the leaders of various manufacturing sites in Japan who use STQA to share supplier-related information and discuss measures to resolve issues.
Example Initiatives
The quality assurance division of Tokyo Electron Technology Solutions is strengthening the acceptance inspection process to allow signs of component non-conformance to be discovered early. Component appearance defects from scratches and dents make up approximately 40% of all non-conformances discovered
during acceptance inspection. As a result of efforts to improve and strengthen component appearance, such as working with suppliers to find the causes and selecting appropriate packaging materials, the target value of 130 ppm (130 nonconforming products in every one million products) was achieved in fiscal year 2022 even though the number of shipments increased. Going forward, we will continue to strengthen cooperation with suppliers and undertake continuous improvement activities.
Quality Education
We are striving to enhance the awareness of every employee toward quality by conducting various education programs. In addition to the basic education on quality that new employees receive, we have also globally rolled out PDCA Education and other programs that target all TEL group employees. In PDCA Education, employees learn about the need for continuous improvement through the four processes of plan, do, check, and act. As of FY2020, 84% of employees had completed this program.
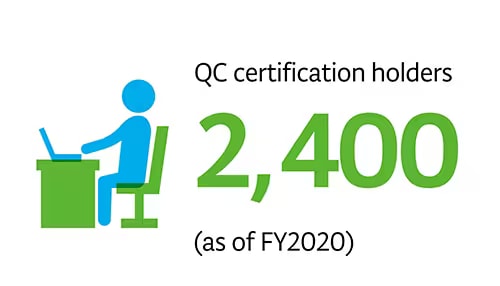
We also implement our own education program, called TEL 6-Step, for employees closely involved in quality control, such as developers, designers, quality managers, and service personnel, through which they acquire a problem-solving model to handle important issues. The program is a modified version of the eight discipline (8D) problem-solving method*1, widely used in quality control, customized to replace our problem-solving process. The program cultivates the ability to resolve problems quickly and to take measures preventing recurrence, by thoroughly investigating the true nature of problems, and determining the technical factors and root causes. As of FY2020, approximately 5,800 employees had attended this program. We also conduct group training targeted at quality control leaders to provide them exercise-based learning opportunities for resolving quality-related issues to further enhance their work improvement skills at production and development sites.
Moreover, so that employees can tackle quality improvement autonomously, we advocate QC certification*2 and encourage them to acquire fundamental skills. Since fiscal year 2012, the number of QC certified employees has increased yearly to approximately 2,400 as of FY2020.
8D problem-solving method: A method for solving problems in quality improvement through eight disciplines or processes
QC certification: Quality management certification operated by the Japanese Standards Association and the Union of Japanese Scientists and Engineers. The total number of certified people nationwide exceeds 580,000 (as of September 2019)