Product competitiveness
Continuously create high value-added next-generation products
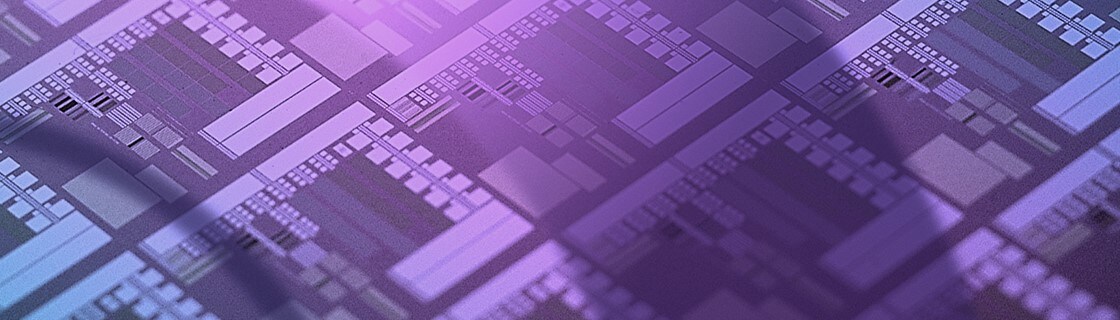
We will expand the following initiatives to “Continuously create high value-added next-generation products.”
- Create the best, high-value-added equipment with innovative technology in a timely manner through the development of product marketing and the global promotion of research and development with an eye on future generations
- Boost competitiveness by assigning personnel at research, development and production sites worldwide, including corporate headquarters, to promote intellectual property (IP) management, and by building IP portfolios aligned with technology and product strategies
- Continuously strive to reduce the environmental impact of equipment and provide technology that contributes to the development of devices with even lower power consumption, to preserve the global environment
- Strengthen product competitiveness by deploying digital transformation, through the use of digital technology as “leverage” to improve added value and efficiency
SDGs initiatives
- Create innovative technologies and contribute to the development of a sustainable society through the promotion of innovation
- Promote inclusive and sustainable industrialization
- Promote scientific research and improve technological capacity in the industrial sector of every country
- Contribute to the reduction of environmental impact company-wide by providing products and services that are conscious of the environment
- Improve resource use efficiency and expand the introduction of clean and environmentally-friendly technologies
- Strengthen global partnerships for sustainable development