Promotion of Improved Productivity
Initiatives of Digital Transformation (DX)
Based on the idea that DX initiatives are a means and an opportunity to achieve our management vision and management plan, and to create corporate value, in January 2021, we formulated the TEL DX Vision and the TEL DX Grand Design.
Through digital technologies, we will promote product transformation and business transformation* to accelerate and strengthen business activities associated with important material management issues.
Product transformation: Contributing to customer value creation in a variety of situations, from development to mass production, business transformation: Improving capital efficiency in a variety of situations, from the product planning stage to maintenance.
TEL DX Grand Design
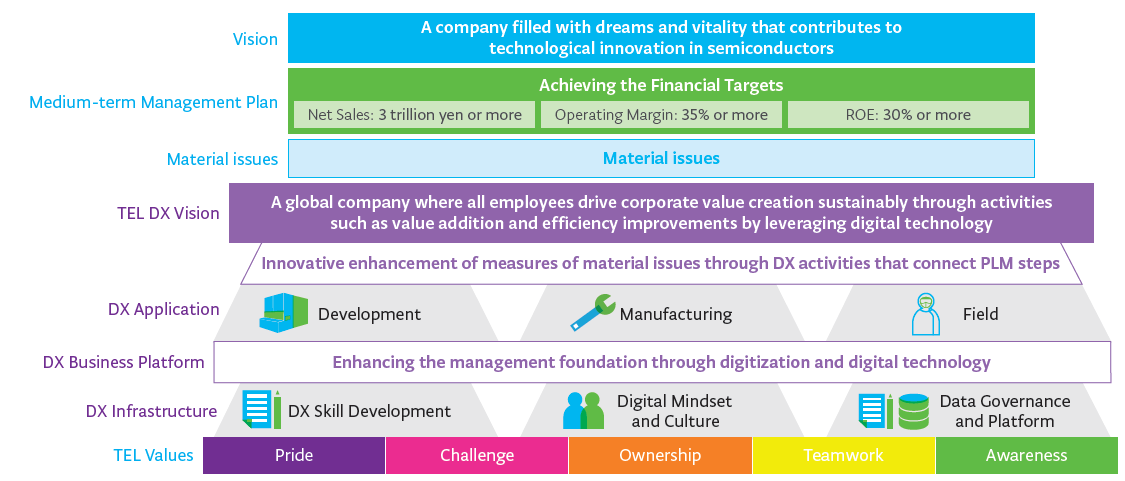
In product transform, we will solve high-level issues while repeating the processes of (1) Recognition (sensing and monitoring), (2) Analysis and prediction, (3) Control and (4) Learning and evolution (autonomous), while aiming to improve customer value.
In addition, in business transform, we will grasp the current state of internal business while envisioning how work should be, and change our work processes by using digital tools, to improve our capital efficiency. We are also promoting the use of digital technology in our management foundation and business support departments, which are necessary to realize these transform initiatives.
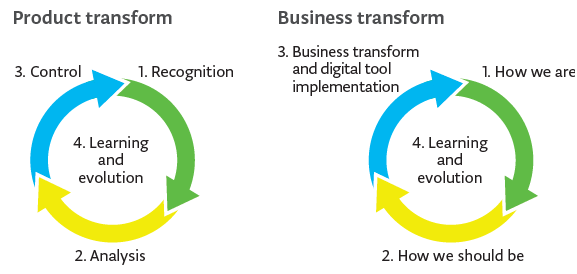
To develop DX human resources, we define the human resources necessary for promoting DX (DX engineers), and formulate a training plan to acquire skills We also create a data platform and data governance, and work to cultivate a digital culture, so that not just DX engineers, but all employees can utilize data in their daily operations. Specifically, this means that we invite outside DX and AI experts to give presentations and hold various digital-related events internally.
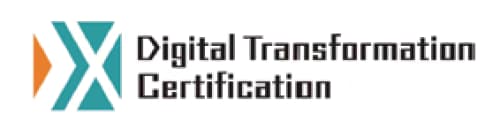
To enable our DX initiatives to lead to the creation of corporate value, we opened the TEL Digital Design Square in Sapporo in November 2020 as the home base for out DX activities. We are also developing leading-edge software technologies needed for semiconductor production and leading-edge digital technologies such as generative AI.
In May 2023, our headquarters was also recognized as a DX-certified business operator under the Digital Transformation Certification initiative established by the Ministry of Economy, Trade and Industry.
Continuous Improvement of Business Operations
We are implementing a new enterprise system (ERP*) to further improve productivity and quality. The purpose of the system is to significantly improve operational efficiency, make management decisions that respond quickly to changes and create new value by utilizing globally integrated information with an eye toward overall digital transformation.
In addition to the headquarters, where the system has already been implemented, we first completed the implementation of this system at overseas subsidiaries and manufacturing sites in Japan in fiscal year 2024. Going forward, we will make maximum use of the knowledge we have gained through the process so far, and will proceed with the implementation of the system to subsequent sites. In addition, we will work with our partner companies to realize a globally integrated system by developing functions and others to improve operational efficiency and further enhance system performance.
Overview of the New Enterprise System
ERP: Enterprise Resource Planning. A system that integrates the core business operations of an enterprise, such as accounting, personnel, production, logistics and sales, for better efficiency and centralized information.

Initiatives for Higher Productivity
As a manufacturer of semiconductors and flat panel display production equipment, we are committed to continuously improving productivity while remaining focused on safety and quality in operations along the entire value chain.
Specifically, under the slogan “Safety First*1,” we are striving to improve the safety and work environments of every person connected with our business activities, and at the same time, we are building quality management systems and pursuing quality improvement throughout the value chain in order to understand the true needs of our customers and to achieve the world’s best quality. We are also conducting company-wide activities for compliance with safety and environmental laws and regulations and to make software development more efficient and smarter.
In manufacturing operations, our current initiatives include labor saving in production through a system that links BOM*2 to MES*3, and transforming production performance into a Digital Twin*4.
Furthermore, to respond swiftly to customer requests and market fluctuations, we have built a production system that centralizes all information related to production, and have developed an IT infrastructure with manufacturing execution system (MES) and a supply chain management (SCM)*5 system.
By utilizing the wide range of data aggregated through these systems in each business operation, we are working on optimizing and streamlining production planning as well as visualizing delivery dates of parts by strengthening information coordination with our suppliers. We are also promoting comprehensive
improvement of business productivity by achieving stronger coordination between sales planning and production/procurement/inventory planning.
Additionally, in our manufacturing and logistics operations, where we deal with a wide variety of components, we are also working on labor savings and efficiency improvements by establishing automated warehouses, introducing a warehousing navigation system and promoting automated inspections.
Safety First: Company slogan that prioritizes the safety of every person connected with our business activities
BOM: Bill Of Materials. This shows the hierarchical structure of the product and includes basic information of each part, including which parts are used to assemble the product.
MES: Manufacturing Execution System. A system for understanding and managing production processes and for providing instructions and support to workers.
Digital Twin: A "Twin in digital space" refers to a technology that copies and replicates various data collected from physical objects in the real world onto a digital space.
Manufacturing execution system (MES) and a supply chain management (SCM): Refer to Continuous Improvement of Business Operations