Tokyo Electron Develops an Extreme Laser Lift Off Technology That Contributes to Innovations in 3D Integration of Advanced Semiconductor Devices
Tokyo Electron (TEL; Head Office: Minato-ku, Tokyo; President: Toshiki Kawai) announced that a development team at Tokyo Electron Kyushu, - the development and manufacturing site for wafer bonder/debonder systems- has developed an Extreme Laser Lift Off (XLO) technology that contributes to innovations in 3D integration of advanced semiconductor devices adopting permanent wafer bonding. This is a new technology for two permanently bonded silicon wafers that uses a laser to separate the top silicon substrate from the bottom substrate with integrated circuit layer.
The progress of digital society is raising expectations for greater improvement in semiconductor chip performance. As a result, the next-generation semiconductors being introduced feature further scaling and higher integration as well as advancements in 3D integration using the permanent wafer-to-wafer bonding technology. In the current permanent wafer bonding sequence, two wafers with integrated circuits on their surface are permanently bonded together before going through a grinding process, in which the top wafer is thinned and removed. Since advanced semiconductor devices require an increasing number of stack layers, there is a growing concern that the grinding process may decrease the yield due to factors such as the stress on wafers while grinding, delaminating of films after grinding and widening of the edge trimming area (which reduces the number of viable chips on a wafer). For these reasons, technological innovation is required with a different approach from grinding technology.
TEL’s breakthrough Extreme Laser Lift Off technology replaces the current wafer thinning and removal process that relies on grinding, thereby enabling removal of the top silicon wafer without the yield concerns associated with the existing process.
The Extreme Laser Lift Off technology simplifies the wafer thinning process by replacing and eliminating multiple existing steps, including backside grinding, polishing and chemical etching of silicon wafer. Compared with the grinding process, the Extreme Laser Lift Off process does not require deionized water, which leads to an over 90% reduction in water consumption and a significant drop in the drain water, contributing to mitigate the environmental load. Furthermore, we are developing a technology to properly treat and reuse the top silicon substrate separated by Extreme Laser Lift Off, which can help reduce the CO2 emissions from wafer fabrication.
Continually adhering to pursue the motto of Best Products, Best Technical Service, TEL will keep contributing to technological innovation in semiconductors. As we celebrated the 60th anniversary of our founding this year, we take this milestone as a new starting point for our further challenge and evolution to contribute to the development of a dream-inspiring society.
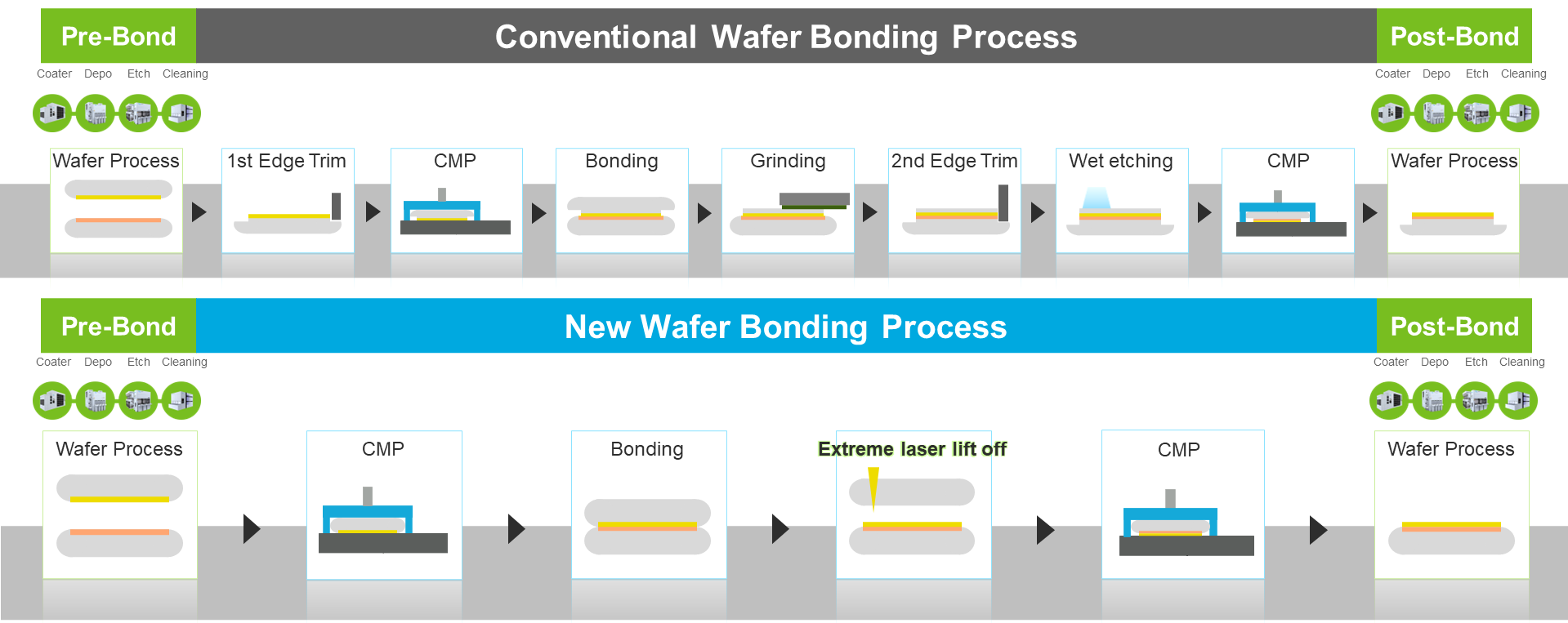
Chart: Permanent wafer bonding process (a comparison of current process with one using Extreme Laser Lift Off technology)
Source: Tokyo Electron
For product purchase queries, please contact
For use of the chart , please contact
Corporate Communication Dept., Tokyo Electron
- tel
- +81-3-5561-7004
- telpr@tel.com